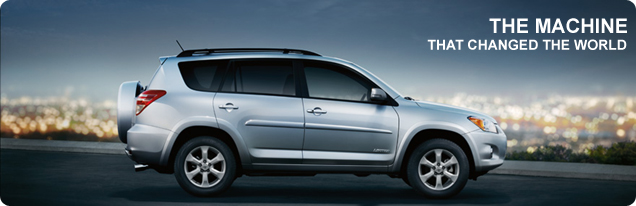
Leading to Lean
The process toward becoming a Lean Enterprise proceeds on three levels through a similar sequence of activities following the Plan-Do-Check-Adjust cycle. The first level is strategic, or company-wide. The second level is plant or location oriented. The third level is process-specific within a location. At each level, an important activity to facilitate planning is to define the current condition with data - establish a measurable baseline for improvement.
Steps for the Development of the Roadmap to Lean Manufacturing

Phase 1: Specify value by Product
Only the customer can define value (Real or Perceived)
• Steps:
Select initial implementation scope
Define customer
Define value - Quality, Schedule, and Target Cost
• Tools
Quality Function Deployment QFD
• Output
The product, customer, and value all defined so as to allow the distinction between value added and non-value added operations.
Phase 2: Identify the Value Stream
Graphic or visual display of all the systems/processes that make up a value stream as the product flows
• Steps:
Record Current State Value Stream
Chart Product and Information Flow
Chart Operator Movement
Chart Tool Movement
Collect Baseline Data
• Tools
Value Stream Map
Spaghetti chart
• Output
A value stream map that shows the entire information and production process as a system with measures of value added and waste for each process.
Phase 3 - Design Production System
• Steps:
Develop a Future State Value Stream Map
Identify Takt Time Requirements
Review Make/Buy Decisions
Plan New Layout
Integrate Suppliers
Design Visual Control System
Estimate and Justify Costs
• Output
A production system design that is ready for incremental implementation.
Phase 4 - Implement Flow
This phase marks the conversion from a batch and queue type of operation to cellular type of operation.
• Steps:
Standardize Operations SOP
Mistake Proof Processes Poka-Yok
Achieve Process Control
Implement TPM Total Productive Maintenance
Implement Self-Inspection
Eliminate/Reduce Waste
Cross Train Workforce
Reduce Set-up Times SMED
Implement Cell Layout
Implement Visual Controls
• Output
Areas within the production system have implemented processes to ensure that production flow has been achieved. In this state individual areas have managed to reduce a significant amount of waste
Phase 5: Strive for Perfection
The various Lean techniques and tools implemented in earlier phases are repeated and refined taking the improvements to the next level.
• Steps:
Standardize Operations SOP
Optimize Quality
Institutionalize 5S
Institute Kaizen Events
Remove System Barriers
Expand TPM -
Evaluate Against Target Metrics
• Output
The outputs of Phase 6 are incremental, continuous, and generally supportive of the Lean transition process
» More Information